Современные торцевые уплотнения вала центробежных компрессоров и нагнетателей
Эксплуатационная надежность турбокомпрессорных машин в значительной степени зависит от работы уплотнительных узлов, герметизирующих вращающийся ротор. Одной из важнейших проблем современного машиностроения является задача создания надежных и герметичных уплотнений роторов центробежных компрессоров. Это обусловлено, с одной стороны, высокими давлениями уплотняемой среды и окружными скоростями в уплотняющем контакте, с другой стороны – очень жесткими требованиями к герметичности и надежности, которые повышаются вместе с ростом параметров.
Традиционно для этой цели используются бесконтактные уплотнения (щелевые, лабиринтные, плавающие кольца и др.). Наиболее применяемые в компрессорах уплотнения с наружным и внутренним плавающими кольцами, между которыми подается запирающее масло под расчетным давлением, достаточно надежны, но не лишены недостатков:
- большие безвозвратные потери масла, особенно при пусках;
- низкий ресурс плавающих колец;
- повышенная загазованность масла в баке;
- колебания перепада давления на внутреннем кольце.
Более перспективными являются торцовые уплотнения, которые обладают высокой герметизирующей способностью, т. е. уровень протечек через них в несколько раз ниже.
Это связано с тем, что гарантированный зазор между уплотняющими поверхностями колец находится в пределах 2…5 мкм, в отличие от щелевых, где зазор достигает десятых долей миллиметра.
Современные двойные уплотнения экономят газ
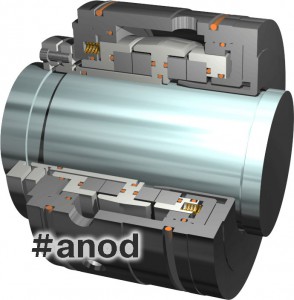
Двойное торцевое газовое уплотнение 100УТДГ
НПЦ «АНОД» в своих уплотнениях для нагнетателей и компрессоров применяет принципиально новые решения в уплотнительной технике, апробированные в оборудовании атомной энергетики, что обеспечивает высокие показатели надежности: длительный ресурс и минимальный уровень протечек.
В ноябре 2001 года НПЦ «АНОД» совместно с АОЗТ «НИКТИТ» (г. Санкт-Петербург) провел стендовые испытания специально разработанного и изготовленного комплекта уплотнений вала центробежного нагнетателя Н47-74-1 в составе агрегата ГПА–4РМ. Высокие параметры работы нагнетателя и небольшой осевой габарит посадочного места заставили применить особые конструктивные решения при проектировании уплотнения. Уплотнение блочной конструкции, двойное, с принудительной циркуляцией затворного масла. С целью обеспечения надежности и высокой герметичности на частотах вращения ротора (7000…11000 об/мин) антифрикционные кольца выполнены из материала с высоким модулем упругости — карбида кремния. Одной из особенностей уплотнения является то, что оно рассчитано на работу в стояночном режиме при давлении до 10 МПа. Агрегат, установленный на КС Касимовского ПХГ, наработал 25 000 часов при более 300 пусках — остановах, безвозвратные потери масла составляют 0,022 кг/час, что на порядок ниже заявленных в техническом задании.
В 2011 году пущены в эксплуатацию холодильные компрессоры Д203ГЦ1-710 на станции охлаждения газа СОГ-4 КС «Ямбургская». Компрессоры изготовлены Сумским МНПО им М. В. Фрунзе и оснащены двойными торцовыми уплотнениями 130УТДГ2. Уплотнения реализовали заветную мечту газовиков: они рассчитаны на работу в длительном стояночном режиме без сброса газа из полости нагнетателя и без включения масляного насоса для поддержания давления масла.
В случае использования двойных торцовых уплотнений масло циркулирует по замкнутому контуру при высоком давлении без сброса его в бак с атмосферным давлением, преодолевая только сопротивление трассы циркуляции. Давление в системе обеспечивается перекачиваемым газом, а мощность насосов расходуется только на прокачку масла при перепаде давления на контурной ступени уплотнения около 0,3 МПа.
Для охлаждения масла в схеме используется теплообменник типа АВО – аппарат воздушного охлаждения, в остальном используется оборудование масляных систем, применяемое в существующих схемах.
Предлагаемая схема маслоснабжения компрессоров может быть реализована при создании новых компрессоров или при выполнении модернизации оборудования, находящегося в эксплуатации. При этом доработок роторов не требуется, двойные торцовые уплотнения устанавливаются вместо существующих уплотнений (щелевых или одинарных торцовых). В корпусах компрессоров требуется выполнение канала для отвода масла из уплотнения.
- уменьшить затраты на техническое обслуживание;
- упростить ряд операций по монтажу, наладке и регулировке уплотнений на объекте; исключаются из конструкции дросселирующие узлы и необходимость тщательной подгонки плавающих колец с минимальными радиальными зазорами;
- обеспечить лучшие вибрационные характеристики в результате эффективного демпфирования колебаний ротора в широком спектре частот;
- уменьшить мощность винтовых насосов высокого давления;
- не сбрасывать перекачиваемый газ из контура компрессора и прилегающих трубопроводов при остановах агрегата.
Опыт проектирования и эксплуатации с 1996 года
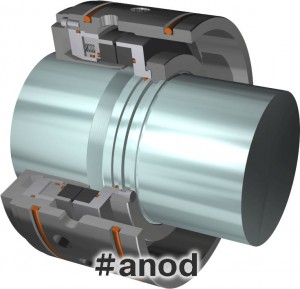
Схема одинарного торцевого газового уплотнения 150УТГ
Отличительной особенностью уплотнений НПЦ «АНОД» с гидрозатвором является не только минимальный уровень протечек (0,05…0,1 кг/ч) масла в перекачиваемый газ, но и высокая его стабильность, независимо от перепада давления, частоты вращения ротора и температуры. Такие высокие показатели качества и надежности обусловлены конструктивными особенностями уплотнений, обеспечивающими постоянство формы и величины зазора в уплотняющем стыке. Поскольку конструкция уплотнения представляет собой сложную систему, состоящую из многих деталей, жестко соединенных между собой и находящуюся под воздействием многих факторов (давления, температуры, центробежных сил, реакции опорных колец и пр.), задача сохранения расчетной формы уплотняющего зазора становится практически неразрешимой. Поэтому, между находящимися в контакте кольцами пары трения и взаимодействующими деталями конструкции сохраняется только связь, необходимая для нормального функционирования узла.
Основными факторами, воздействующими на элементы уплотнения центробежных нагнетателей и компрессоров, являются частота вращения ротора, вибрация, осевые перемещения ротора, перепад давления между запирающим маслом и уплотняемым газом, температура уплотняемого газа.
При разработке уплотнений для такого класса механизмов НПЦ «АНОД» придерживается следующих принципов проектирования:
- минимальные диаметральные размеры вращающихся элементов, что значительно снижает потери на трение,
- поперечное сечение кольца — квадрат или прямоугольник, исходные поверхности колец, при этом, практически не искажаются под действием статического давления, температуры и центробежных сил,
- для защиты вращающегося кольца от действия центробежных сил рекомендуется посадка его в опорный элемент с расчетным натягом по наружному диаметру, а также использование бандажа из металла с близким по величине коэффициентом термического расширения, установленного на вращающееся кольцо,
- допуск параллельности рабочих поверхностей кольца пары трения составляет 0,005…0,008 мм,
- отсутствует биение опорного торца вращающегося элемента с установленным в нем кольцом пары трения,
- вращающееся кольцо пары трения имеет угловую подвижность для компенсации перекосов ротора в радиальных опорах при переходных режимах работы нагнетателя (компрессора),
- перепад давления между запирающим маслом и уплотняемым газом составляет от 0,1 до 0,6 МПа,
- тепло-гидравлический расчет для определения расхода запирающего масла через затворную камеру выполняется с учетом мощности тепловыделения уплотнением и температурных условий в месте размещения уплотнения;
- выполняется прочностной расчет уплотнения с целью анализа напряженно-деформированного состояния элементов от действия давления среды, температуры, механических нагрузок и центробежных сил (программа ANSYS).
- блочное исполнение (в состоянии монтажной готовности);
- выполняется подбор материалов (металл, резина, пара трения);
- установка в оборудование без какой-либо доработки посадочных мест в корпусе и на валу;
- поставка уплотнений в комплекте с инструментом и приспособлениями для монтажа.
НПЦ «АНОД» с 1996 года занимается оснащением масляными уплотнениями центробежных нагнетателей магистральных газопроводов ОАО «ГАЗПРОМ». В настоящее время НПЦ «АНОД» тиражирует уплотнения вала для нагнетателей типа: 235-21-1 (130УТГ1), 235-28-1(150УТГ), 370-14-1(120УТГ), 370-18-1(140УТГ), 520-12-1(145УТГ), 650-21-2(200УТГ). Для каждого типа нагнетателя проектировалось уплотнение с элементами унификации: типоразмеры резиновых колец, размеры колец пары трения, крепежные изделия. В настоящее время более 2000 уплотнений производства НПЦ «АНОД» эксплуатируются в составе нагнетателей газоперекачивающего оборудования предприятий ОАО «ГАЗПРОМ». Согласно справкам этих предприятий усредненная величина безвозвратных потерь масла в перекачиваемый газ составляет 0,12…0,2 кг/час на нагнетатель, а годовая экономия турбинного масла исчисляется десятками тонн. Блочное исполнение уплотнений, применение инструмента и специальной оснастки гарантирует качественный и безошибочный монтаж.
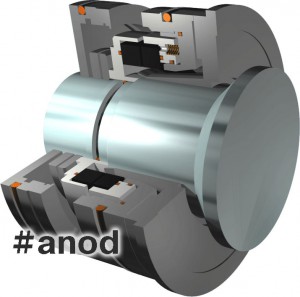
Одинарное торцевое газовое уплотнение 130УТГ1
Следует отметить, что уплотнения успешно работают в диапазоне окружных скоростей 40…50 м/с, перепада давления «масло-газ» до 6 кгс/см2 и давлении перекачиваемого газа до 80 кгс/см2 при уровне протечек масла 0,05…0,1 кг/ч. Конструкция уплотнений обеспечивает ресурс уплотнений до 50 000 часов при мелком ремонте: замена резиновых колец, замена деталей поводкового устройства, при необходимости — притирка пар трения.
Материал пар трения – карбид кремния. Температуростойкая резина марки СБ-26 гарантирует работоспособность уплотнения в течение назначенного ресурса уплотнения.
Одна из значимых работ НПЦ «АНОД» – разработка торцовых уплотнений типа 110УТГП, предназначенных для замены щелевых уплотнений в высокооборотных (8300 об/мин.) нагнетателях природного газа НЦ-6,3. Уплотнение представляет собой блок, состоящий из корпуса со сквозными отверстиями для прохода масла, передней и задней крышек. Внутри блока размещаются: основное — торцовое одинарное, и вспомогательное – щелевое, уплотнения. Торцовое уплотнение имеет подвижный уплотняющий контакт между двумя кольцами пары трения, одно из которых размещено во вращающейся вместе с валом втулке, а другое – неподвижное, установлено в обойме, поджимаемой комплектом пружин.
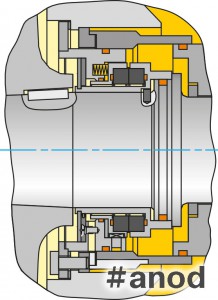
Схема одинарного торцового уплотнения газового 98УТГ
Вспомогательное щелевое уплотнение выполнено в виде обоймы, содержащей два плавающих кольца, внутренний диаметр которых образует с хвостовиком вращающейся втулки радиально-щелевое уплотнение. Каждое плавающее кольцо торцевым пояском контактирует с притертой поверхностью закаленного седла Г-образной формы, имеет возможность перемещаться в радиальном и осевом направлениях и подвешено на 4 радиально установленные пружины сжатия. Внутренняя поверхность плавающих колец имеет баббитовую наплавку, а ответная поверхность хвостовика вращающейся втулки – износостойкое покрытие.
Основное торцовое и вспомогательное щелевое уплотнения разделяет кольцевая затворная камера, в которую поступает запирающее масло под давлением, превышающим давление перекачиваемого газа на величину перепада «масло – газ» — 0,1…0,6 МПа, обеспечиваемого регулятором перепада давления (РПД).
Отличительной особенностью данного щелевого уплотнения является то, что осевая длина плавающего кольца уменьшена до 0,15 диаметра вала, что позволило уменьшить массу кольца и избавиться от реакции на перекосы вала. При этом перепад давления между затворной камерой и атмосферой делится поровну между двумя кольцами, поэтому осевая сила, действующая на каждое кольцо, снижается вдвое, а значит, меньше удельное контактное давление на торцовом уплотняющем пояске. Пружины сжатия, на которые подвешено плавающее кольцо концентрично оси вращения ротора, расставлены таким образом, что гидродинамические центрирующие силы превалируют по величине над силами трения в торцовом стыке, а собственная частота кольца существенно повышается. Радиальный зазор между плавающим кольцом и вращающейся втулкой выбирается из условия обеспечения расхода запирающего масла достаточного для охлаждения основного и щелевого уплотнений.
Благодаря конструктивным мерам (уменьшение диаметра вращающихся деталей основного уплотнения, применение новых материалов) затраты на трение вращающихся элементов с кольцами пар трения сведены к минимуму и составляют не более 3,5 кВт на уплотнение. Вращающаяся втулка уплотнения фиксируется на роторе специальным цанговым зажимом. Все элементы уплотнения, устанавливаемые на ротор нагнетателя, изготовлены с высокой точностью и не требуют балансировки в составе ротора.
Для проверки правильности концепции разработки и изготовления опытного комплекта (2 шт.) были проведены испытания по специальной программе в составе нагнетателя НЦ — 6,3 – 56/1,45 в Приокском ЛПУМГ ООО «Газпромтрансгаз Н. Новгород». Испытания подтвердили работоспособность разработанного уплотнения в штатных условиях и были получены следующие результаты:
- протечки масла в газ на нагнетатель составили 0,24 кг/ч,
- полное отсутствие загазованности масла,
- высокая стабильность установленного 0,15 МПа перепада давления «масло – газ»,
- подогрев масла тепловыделениями уплотнения 22…25ºС,
- износ баббитовой наплавки плавающих колец и колец пар трения торцового уплотнения отсутствует,
- производительность насоса подачи запирающего масла нагнетателя достаточна для обеспечения температурного режима уплотнений.
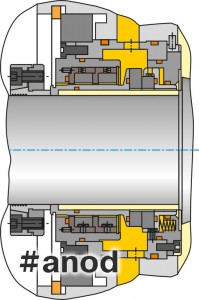
Схема комбинированного торцевого газового уплотнения 110УТГП
Первый комплект уплотнений 110УТГП эксплуатируется в составе нагнетателя НЦ-6,3-56/1,45 на КС «Ворсменская» Приокского ЛПУМГ ООО «Газпром трансгаз Н. Новгород» с 10.05.2000 года.
В феврале 2002 года уплотнения прошли межведомственные испытания со следующими результатами: протечки масла в газ на нагнетатель составили 0,24 кг/ч против 0,4…0,8 со штатным уплотнением. Наработка агрегата на настоящий момент составляет более 40 000 часов. Единственная ревизия данных уплотнений проводилась после наработки 36 000 часов. Были заменены резиновые уплотнительные кольца и притерты кольца пары трения.
Конструкция данного уплотнения, как и всех прочих, защищена патентом РФ.
Результаты эксплуатации уплотнения вала нагнетателя НЦ-6,3-56/1,45 доказывают, что разработка торцовых уплотнений с большими окружными скоростями (более 50 м/с) и низким уровнем утечек затворного масла — разрешимая задача.
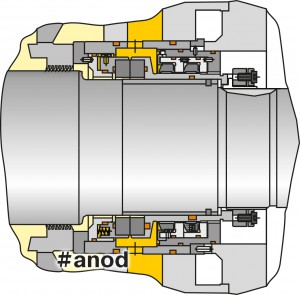
Схема комбинированного торцевого газового уплотнения 160УТГП1
На базе опыта, полученного в процессе разработки конструкции уплотнения для нагнетателя НЦ-6,3-56/1,45, НПЦ «АНОД» по заданию НПО «ИСКРА» (г. Пермь) разработал и поставил 8 комплектов торцовых уплотнений типа 150УТГП и 150УТГП1 к сменным проточным частям СПЧ76/1,44 и СПЧ76/1,35 нагнетателей ГПА-Ц-16 (ноябрь 2001г., декабрь 2002г.) для КС «Кунгурская», КС «Новокомсомольская», КС «Ныдинская». Конструктивный подход остался прежним, т.е. уплотнительный узел состоит из уплотнения одинарного торцового и вспомогательного щелевого с двумя плавающими кольцами. Приемо-сдаточные испытания первых двух комплектов уплотнений для СПЧ76/1,44 выполнены на стенде предприятия «Компрессорный Комплекс» (г. Санкт-Петербург) при перепаде давления «масло – газ» (0,3…0,4 МПа) на номинальной частоте вращения ротора в течение 12 часов.
С высокими показателями надежности работают уплотнения 150УТГП3 00.00 в составе агрегатов ГПУ-16 на линейной ГКС Пильнинского ЛПУМГ ООО «Газпром трансгаз Н. Новгород». Наработка первых комплектов уплотнений превышает 40 000 часов, удельный расход масла на нагнетатель — не более 0,2 кг/ч. Колебания перепада давления «масло-газ» — в пределах 0,04…0,06 кг/см2.
В 2012 годуреализована программа на КС Ставропольского УПХГ по полной замене щелевых уплотнений на торцовые типа 125УТГП в нагнетателях Ц-6,3/51 и Ц-6,3/100. Основные требования, предъявляемые к нагнетателям, эксплуатирующимся на станциях ПХГ — это минимальные утечки масла и повышенная надежность оборудования.
Наряду с проектированием и изготовлением масляных уплотнений в НПЦ «АНОД» ведутся работы в новом направлении – освоении производства сухих газодинамических уплотнений (СГУ) совместно с предприятием «Грейс-инжиниринг». В настоящее время предлагаем поставку запасных частей, выполнение ремонта, обслуживания и испытаний систем СГУ любых производителей, включая зарубежных.
Работы НПЦ «АНОД» в области уплотнительной техники доказывают возможность применения торцовых уплотнений на окружных скоростях до 80м/с, давлении — до 10,0МПа и температуре уплотняемой среды — до 200°С. Уплотнения с гидрозатвором менее критичны к перекосам ротора в подшипниковых опорах и высоким уровням вибрации (до 50 мкм). Уровень протечек масла в перекачиваемый газ уплотнений производства НПЦ «АНОД» почти на порядок меньше чем у существующих уплотнений. При многих преимуществах известных сухих уплотнений, малорасходные уплотнения с гидрозатвором способны с достаточной надежностью и малыми затратами герметизировать валы высокооборотных механизмов и, таким образом, продлить эксплуатацию достаточно большой части парка газоперекачивающего оборудования ОАО «ГАЗПРОМ» и компрессоров предприятий нефтехимических производств.
Сокращаем затраты на эксплуатацию и ремонт оборудования
С 1996 года НПЦ «АНОД» изготовил и поставил газотранспортным предприятиям ОАО «Газпром» более 2000 комплектов торцовых уплотнений для ГПА.
За указанный период конструкция торцовых уплотнений постоянно модернизировалась в целях повышения надежности и исходя из появления новых современных материалов.
В 2012 году в целях повышения качества и увеличения межремонтного ресурса конструкция уплотнений типа УТГ и УТГП была модернизирована. Был сменен поставщик основных комплектующих деталей — колец из карбидо-кремниевого материала на иностранную фирму, одного из мировых лидеров по их изготовлению, т. к. отечественные производители указанных изделий не обеспечивают необходимое качество материала. Исходя из пожеланий предприятий, эксплуатирующих ГПА, комплектуем каждое уплотнение дополнительным комплектом монтажных РТИ (резиновых колец).
В связи с вышеизложенными и во исполнение Плана мероприятий Председателя Правительства РФ Д. А. Медведева № 6732п-П9 от 11.11.2013г. и письма ОАО «Газпром» исх. № 03-2293 от 12.12.2013 НПЦ «АНОД» предлагает особо обратить внимание на возможность уменьшения издержек на ремонт ГПА и рассмотреть вопрос проведения ремонтов имеющихся в эксплуатации торцовых уплотнений с одновременным выполнением их модернизации. Стоимость ремонта и модернизации торцовых уплотнений значительно ниже цен новых уплотнений.